“Solving the Riddle of Steel”
By Dan Shea
“The secret of steel has always carried with it a mystery. You must learn its riddle, Conan. You must learn its discipline. For no one—no one in this world can you trust. Not men, not women, not beasts. But steel; this you can trust.”—Conan the Barbarian’s father as he points to a sword he’d made.
It’s probable that most English-speaking readers of SADJ have seen John Milius’ adaptation of the Robert E. Howard stories in “Conan the Barbarian.” Entrenched in our modern martial culture, many of us jokingly quote the movie’s lines, because on an elemental level, it speaks truths to fighting men. The Riddle of Steel—it calls us; we philosophize around it, perhaps jokingly, but there is always a truth hidden in the words. At the core, the various answers appear to be contradictory: First, steel is strong and flesh is weak; Second, the opposite—flesh that wields the steel is strong, and steel is nothing without that; Third and perhaps most important, that the will and determination to use the steel in righteous endeavor is the true strength.
In fact, the Riddle of Steel is solved if all three of those are blended into one truth.
In the United States military, we have a group called SOCOM (USSOCOM)—it is comprised of warriors, working for warriors, to enhance their fighting capabilities. At the risk of being trite, this brotherhood is dedicated to using steel in righteous endeavor, and they train hard to have the physical capabilities to wield the steel, and, of course, their weapons are almost always the best that can be found. Started in 1987 to create a unified command for US Army, Navy, Marine and Air Force special operations groups, a significant part of the mission is new equipment.
In the modern fighting arena, in that hardened place that is called “downrange,” increasing distances of engagement as well as armoring of targets are challenging the warriors. There have been many attempts to address this—not all failed, but few are chosen by the warrior leadership. Barrett Firearms has been chosen more than once …
One item of “steel” that has been chosen by SOCOM to be at the forefront for these warriors, is the newly adopted Mk22 Mod 0 “ASR” Advanced Sniper Rifle—the next evolution of Barrett Firearms Manufacturing’s MRAD rifle system. For SOCOM, where the physical strength and the righteous will are, the Mk22 very nicely completes the triad of the Riddle of Steel.
Barrett’s MRAD Concept
To understand the Barrett MRAD (Multi-Role Adaptive Design) rifle requires some background information. You can get the spec sheet story by searching “MRAD” online; our job at SADJ is to help the readers really understand the Mk22 system. Creating an accurate rifle that can interchange calibers is a unique challenge. Easy enough to change out a barrel and bolt, but to do so and maintain true precision accuracy, that is an entirely different matter. There have been many systems with interchangeable barrels, especially in machine guns; but those are area weapons, not point weapons. This has to be made in a man-portable manner as well, so steel is too heavy a choice for the chassis.
“The Riddle of Aluminum” doesn’t sound quite so interesting, but in fact that is where Barrett’s engineers went to create the MRAD/Mk22. There are eight “Thousand” series of aluminum alloys and some oddities; each has a commonality within its group. Pure aluminum is a very soft metal and requires additives (alloy) and treatments to gain strength. What are called the 7000 series aluminums are aluminum/zinc alloys with percentages of other metals that dictate the actual number. When searching for a material to CNC mill the MRAD monolithic receiver, the light weight of alloys and reasonable cost are a quick draw; but out of the hundreds of potential alloys, which one?
Starting after World War II, an alloy used by many in the aircraft industry is 7075 (a Japanese mix). It is an alloy of 90% Aluminum, 5.6% Zinc, 2.5% Magnesium, 1.6% Copper and 0.23% Chromium; some various tiny amounts of other metals are used as well. This lightweight, easily tempered and machined 7075 is ideal for use in firearms, and 6061 (6xxx—Silicon as main additive, not Zinc) and 7075 are alloys favored in the “AR” industry. Almost every written description of an AR will say “7075 T6 Aluminum” as if it was magical transition of knowledge to a reader. Actually, in the 5.56mm AR platforms, the real benefits of 7075 don’t fully show up. However, Barrett’s engineers are smart enough to know those other attributes solve almost every issue the MRAD faced, and in particular, the split collet nature of the barrel clamping. More on that later.
After cold rolling (adding about 4–6 times the strength) we get to the second part of the magical “7075 T6” invocation, the T6, which is the tempering. In the case of Temper 6 the 7075 is heated to 840ºF (450ºC) for approximately 2 hours, solution quenched, and an artificial “ageing” is physically done by resting at 250ºF (120ºC) for 24 hours (yes, this is a heat treatment). Of the many treatments that can be done, this method (called precipitation strengthening) ensures that the precipitates (tiny particles less than 0.001mm in diameter composed of aluminum and the added alloy metals) forming inside grains and on the grain boundaries produce excellent mechanical strength all through the material and add excellent surface-wear resistance. This is where the phenomenal elongation tolerance of 7075 T6 comes in. But that’s not the best thing…
“OK, Dan, so what is this about the split collet and Barrett engineers?” 7075 with a T6 temper has excellent tensile strength (74,000–78,000 psi) and yield strength of 63,000–69,000 psi. This is all great news for the 5.56mm, 6.5mm and 7.62mm AR builds, but it is the elongation tolerance before breaking of up to 11% that caught the Barrett engineers’ eyes. This is the exact right material tolerance (and heat tolerance) for heavier calibers like the Lapua and Norma Magnums.
The icing on that cake is that with changing calibers, using a split-collet-style clamp built into the upper receiver, the material must elongate and clamp, over and over, maintaining its original form on each return. 7075 T6 is ideal for this.
There are many parts to the MRAD as presented by Barrett, but the most critical is maintaining the accuracy in different barrels that are field changeable. The split collet is the key.
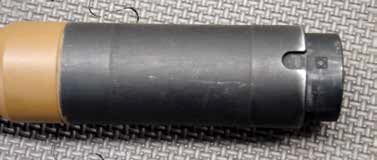
Why tighten to exactly 140 inch-pounds (in-lb)? We go back to the Riddle of Aluminum and that 11% maximum flex before breakage on 7075 T6. We don’t want to flex anywhere near that much, but seating a barrel in an accurate rifle must be done precisely in order to lessen barrel harmonics. Accuracy comes from tightly repeatable events in the physics of the rifle. Get rid of variables in barrel harmonics; tighten them up; shoot a tighter group. In discussion with Barrett, they indicated that when tightening up over 90 in-lb on these screws the group stabilized, and at 140 in-lb, the barrel was supported perfectly, the aluminum sides of the collet area were not overstressed, and the steel screws didn’t distort the threads in the aluminum. Thus, 3.5 inches of 360-degree-supported barrel clamped properly to rigidify it with the monolithic receiver results in the ability to have extreme accuracy from a field changeable rifle. This is the real heart of the rifle.
“The MRAD itself is a manually operated bolt-action rifle fed from a 10-round detachable magazine. It is designed to be a rugged, configurable, precision rifle system; the MRAD can quickly be converted to multiple calibers or barrel lengths. With M-LO[K] mounting slots at 3, 6, and 9 o’clock, its handguard offers a rigid, highly adaptable interface for attachment of rails, electro-optics and other accessories.”—Barrett manual description
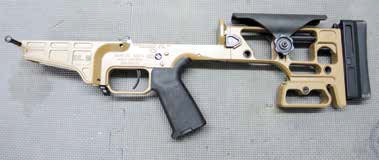
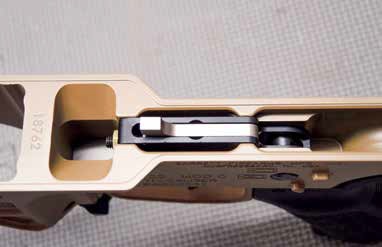
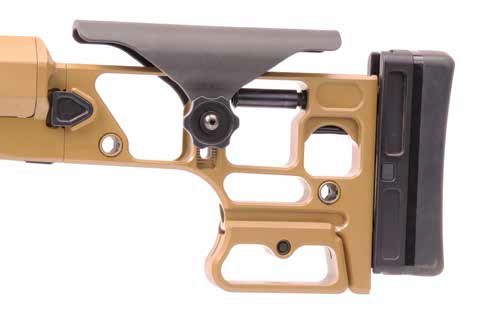
[su_custom_gallery source=”media: 83382,83383″ limit=”40″ link=”image” width=”220″ height=”170″ title=”never”]
Magazines
Longtime readers know this author is a magazine fanatic. Feeding the weapons is often one of the hardest parts of weapon design, particularly in semi- or fully automatic firearms. In the case of a bolt action, it’s not as complex, but it still must be perfect, or you will experience misfeeds. The 10-round MRAD magazine is perfectly designed for presentation and in four basic flavors to properly present cartridges of different length/shoulder location. A properly treated flat spring is used to keep even presentation of the follower, ensuring the cartridge ramps into the chamber without cant.
The first MRAD (now called the Large Breech gun) was in .338 Lapua Magnum, and the magazine has no identification letter and zero ribs on it. After the MRAD was fully developed in different calibers, a system was needed for visual and tactile identification. The Mk22 comes with C- and D-type magazines:
A: .338 Lapua Magnum 6 ribs
B: .300 Win Mag/7mm Rem Mag/.300 PRC 4 ribs
C: .308/6.5 Creedmoor/.260 Rem 3 ribs
D: .338 Norma Magnum and .300 Norma Magnum 6 ribs
The obvious question to end users is whether A and D magazines are interchangeable—no, not reliably. The D magazine is specifically designed to accommodate the shorter shoulder location of the .338 Norma Magnum and .300 Norma Magnum cartridges; you could feed them in the A magazine but probably lose some reliability in feeding. Vice versa, if you had the .338 Lapua Magnum conversion kit for the Mk22, which is after all an MRAD, the A magazine would be needed.


The ASR Award
Date: 03/11/2019
Issued From: HQ USSOCOM – Tampa, FL
Contract #: H9240319D0002
System: Barrett MRAD Rifle System
This is a 5-year Indefinite Delivery/Indefinite Quantity (IDIQ) contract for the Advanced Sniper Rifle and various components identified herein including three barrels in the calibers listed below, spare parts and Barrett AML338 suppressors. No optics are included.
The maximum quantity that shall be purchased is a total of 2,675 units.
The maximum contract value for all orders issued shall not exceed $49,936,299.50.
Calibers: .338 Norma Mag; .300 Norma Mag; 7.62x51mm
Mk22 Mod 0: The Changes from Other Programs
In the first place, the Mk22 does not need the large breech to small breech conversion unit—that was only on the early MRADs in .338 Lapua Magnum to smaller calibers when Barrett added them, and the Mk22 is purpose-designed from the current MRAD, using one homogenous breech for all calibers. The calibers in the Mk22 Mod 0 are the following and no others. There are other USG and DoD groups that add the .300 PRC or 6.5mm Creedmoor kit, but not for ASR. Could you add them? Yes, but it’s not currently authorized in the Mk22.
[su_table responsive=”yes”]
Caliber | Barrel Length | Barrel Profile | Twist Rate | Overall Length | Weight |
.338 NM | 27in | Fluted 1in | 9.4in | 50.625in | 15.2lb |
.300 NM | 26in | Fluted 1in | 8in | 49.625in | 15.1lb |
7.62×51 | 20in | Fluted 1in | 8in | 43.625in | 13.9lb |
[/su_table]
The Mk22 rifle uses an M-LOK system as opposed to Barrett’s proprietary system on the MRAD. The Mk22 has the toggle bolt disassembly and a captive bolt pin.
The Mk22 Mod 0 is in the above calibers only, uses the Harris 6- to 9-inch bipod with a cant dial lock and is Coyote in color. The US Navy MRAD is Flat Dark Earth in .300 PRC and also uses the Harris bipod. The Mk22 does not use a monopod, but the bag rider is included. DoD MRAD issues the Accu-Shot monopod and no bag rider. Regarding the cheek piece, the Mk22 has the positive lock with increments, and the DoD MRAD has a friction lock with free adjustment. Several other differences are that the Mk22 safety has pictograms, and the DoD MRAD is S/F red and white; the trigger for Mk22 is fixed as I mentioned, but the DoD MRAD has a fully adjustable trigger that bottoms out at 1.75 pounds; and the Mk22 barrels are fluted stainless steel, DoD MRAD barrels are not fluted and are carbon fiber constructs. There are a lot of small changes and variations between the Mk22 and the DoD MRAD, but that’s not really our subject here.
[su_image_carousel source=”media: 83390,83391″ limit=”2″ slides_style=”minimal” crop=”16:9″ spacing=”no” dots=”no” link=”lightbox” target=”self” autoplay=”5″ image_size=”thumbnail”]
In addition to the MRAD and manufacturer markings, the Mk22 Mod 0 has US markings on it for issue model, etc.
USSOCOM Advanced Sniper Rifle Requirements
- Must be convertible to fire 7.62mm NATO, .300 Norma Magnum and .338 Norma Magnum cartridges.
- Must not exceed 17 pounds with an empty magazine but is ideally 13 pounds or less.
- Must not exceed 50 inches when fully extended, but is ideally 40 inches.
- Must not exceed 40 inches when collapsed for transport, but is ideally 36 inches.
- Must perform with at least 1 MOA accuracy for the 7.62 NATO and .300 Norma Magnum at 300 yards. Ideally .5 MOA.
- Must perform with at least 2.5 MOA accuracy for the .338 Norma Magnum at 300 yards. Ideally 1.5 MOA.
- Must have a modular flash or sound suppressor.
Calibers
Recently, the SOF community has tried a variety of calibers. The list is dizzying, and if you imagine the testing that has been done, it has occupied a lot of procurement people and design engineers, as well as end users. Here are just a few.
- 6mm Creedmoor
- 6.5mm Creedmoor
- 6.5mm Grendel
- .260 Remington
- .264 USA
- 6.8mm SPC
- .300 PRC
- .300 Norma Magnum
- .338 Norma Magnum
- .338 Lapua Magnum
- And now, 6mm ARC
Jimmie Sloan—Changing the Course
As the rest of the military/LE community (and this author) were variously adopting .338 Lapua Magnum and .300 Win Mag and finding some issues with these calibers in field use (not reliability, other issues), a parallel development had been going on in Willis, Texas. A very devoted long-range shooter named Mr. Jimmie Sloan was working on some new long-range loads, starting about 2005.
To some, Jimmie comes off more than “a little bit country,” and his down-home euphemisms might camouflage the brilliant mind inside there. Frequently, the most interesting leaps forward in technology come from a genius working in his garage—John Browning’s barn/workshop, Gene Stoner’s designs started in his garage, and heck, Carbine Williams did the M1 Carbine in jail!
Rumor has it, a room full of school-taught mechanical engineers tried to have a bit of fun at Jimmie’s expense, and it didn’t work out the way they expected. I asked Jimmie about it; he said, “I told them I didn’t have the schooling they did, but I had 50 years of experience designing, studying and shooting every day, and that over 8 years I hand-made brass and over 190,000 rounds of what became .338 Norma Magnum and made sure of every level of performance. I then asked them how many of their college degrees concentrated on ballistics, ammunition and firearms design. You could hear the crickets.”
The hard fact is, getting a degree in mechanical engineering is not a key to being able to design firearms—many graduating students find out very quickly that the firearms world is basically OJT. You might have training in metals, materials, even heat engines (that’s what firearms basically are) and ME101, but you need to apprentice all over again to be in firearms/ammunition design. The US education system simply doesn’t have firearms design in the curriculum. You can hope to work with someone who has 50 years’ experience and is willing to share it. You have to get your hands dirty. Besides, as the late Jim Schatz used to say, “Any day at the range beats a day at the office!”
Jimmie’s original designs used 240-grain (gr) MatchKing and 230-gr Berger bullets in the .300 Norma Magnum and 230-gr Berger bullets in the .338 Norma Magnum. The performance was superb, with barrel life in the 3,000-plus rounds. These are all excellent projectiles, and Jimmie designed the cartridges for the performance he wanted. Jimmie worked with General Dynamics on their Medium Machine Gun in .338 Norma Magnum, helping get that program moving.
Rumor also has it that one of the government arsenals changed the .300 projectile to a 215-grain and opened up the chamber, with resulting loss of performance and knocking barrel life down to 700 rounds or so. Jimmie’s reply is the eternal designer’s lament: “I gave you a balanced system; you changed something and then complained about the symptoms.”
In any event, the .300 Norma Magnum adopted now has a 215-grain OTM projectile, but Barrett ensured the chamber is “right,” and they’re getting 3,000-plus rounds life. The Barrett engineers worked with JGS Precision for chamber reamers on the MRAD and Mk22 programs (jgsprecision.com).
We should note here that Jimmie worked with Dave Kiff at Pacific Tool & Gauge (PTG) for much of his chamber design/reamers during the design project (pacifictoolandgauge.com). The headspace gauges this author used in the testing were PTG also. We checked headspace after barrel changes of course, as we got used to the system.
Ammo, Ammo, Ammo!
One of the most helpful ammunition companies in the US regarding law enforcement and special operations cartridges is Black Hills Ammunition (BH ammo) (black-hills.com). Started in 1981, Black Hills is synonymous with quality and reliability. This author has known Black Hills founder Jeff Hoffman for decades and has supplied numerous government contracts with BH ammo. Jeff was an active end user, is still a shooter, knows the needs and has the commitment to the end users. The BH ammo is solid, reliable and extremely accurate, and Jeff’s company worked very hard to come up with the loads needed for many other SOCOM projects as well as the Mk22 system. (Jeff was the 2010 recipient of the GySgt. Carlos Hathcock Award from NDIA Small Arms Committee.)
[su_image_carousel source=”media: 83392,83393,83394,83395,83396″ limit=”5″ slides_style=”minimal” crop=”none” captions=”yes” dots=”no” link=”lightbox” target=”self” autoplay=”5″ image_size=”thumbnail”]
Jeff was kind enough to send us a variety of the 7.62x51mm, .300 Norma Magnum and .338 Norma Magnum rounds exactly as used for the ASR program, and that is what we used in our testing. The Black Hills 7.62x51mm is legendary, a superbly accurate 175-grain projectile that is considered even with, if not better than, the military issue M118LR cartridge. In fact, many military and OGA groups use the Black Hills ammo. The .300 Norma Magnum and .338 Norma Magnum supplied to us show the clear results of what SOCOM was looking for during development—see the target section of this article. During development of the Mk22 system, the government awarded a sole-source contract to load reference ammunition to Black Hills. Part of that ammunition contract included a “surrogate” cartridge in .338 Norma loaded with the Sierra 300-grain OTM MatchKing that rifle manufacturers could use in development of the .338 Norma barrel for the system. This was done because of the expense of the AP-loaded cartridge and the close ballistic match between the 300-grain Sierra and the Lapua AP529 projectile. So, in short, there are two different projectiles that have been loaded in .338 Norma: the AP529 and the Sierra 300-grain OTM MatchKing. Only the AP529 is designated as the projectile in XM1162 (.338 Norma Magnum cartridge for the ASR). Many end users want the non-AP round to be adopted also, for use on ranges that can’t accept the AP round.
We also used some of the RUAG 7.62x52mm SWISS P Precision ammunition; longtime readers of SADJ will remember that in 2019 this author tested their palette of 7.62 offerings—seven various tactical rounds that have different jobs, but match point of impact; a truly desirable attribute. Unfortunately, RUAG was not in the competition, but it performed as well as expected.
The ammunition contract to supply the Mk22 Mod 0 “ASR” program did not go to Black Hills; earlier this year it was awarded to Ultra Defense Corp. Ultra Defense, as contract holder, has awarded a subcontract to Capstone Precision Group for manufacturing the cartridges. Capstone will be assembling the cartridges from subcontracted components—Capstone is the US sole distributor for Berger, Lapua, SK and Vihtavuori, among others. The single-year SOCOM agreement is for approximately 1 million rounds of ammunition: 800,000 rounds of .300 Norma Magnum with 215-grain OTM Hybrid Berger projectiles and Lapua-made cases. There will be 200,000 rounds of .338 Norma Magnum and 300-grain AP529 projectiles—both projectiles and cases are from Lapua, a NAMMO company, the AP529 is a NAMMO product and is NOT an OTMHC (Open Tip Match with a Hardened Core) as in numerous publications; it is an Armor Piercing Full Metal Jacket round with Tungsten Carbide Core. Excellent choice, in this author’s opinion, and more importantly the choice of the experts at SOCOM who exhaustively studied and fired tens of thousands of rounds. You can see the results on the targets later in this article. (Ultra Defense is sending SADJ some of the issue ammo for a separate test.)
Optically Speaking
[su_list]
- Eyepiece
- Eyepiece lock ring
- Power throw lever
- Power zoom ring
- ZeroStop™ elevation adjustment
- Contract-specific UltraMount
- Contract-specific removable laser platform
- Capped windage adjustment and battery compartment (Opposite side: Parallax adjustment)
- Objective/Objective lens
[/su_list]
[su_custom_gallery source=”media: 83423,83424″ limit=”3″ link=”image” width=”220″ height=”170″ title=”never”]
The days of putting rounds on target with open sights are long in the past. I’m not saying that no one shoots open sights; most shooters have favorite Garands or ‘03s they can ring a gong or cut an impressive group with. The fact is that in military and LE scenarios, accuracy is king, lives are on the line, and high-grade optical sights, opto-electronics and the training to use them are the way to get there. The operator pulling the trigger and the chain of command up-hill have to answer for the accuracy of the shot and where the projectile lands, among other issues in this very complicated world.
The optic for the Mk22 PVPS (Precision Variable Power Scope) was not contracted with Barrett; but this is a system, and the chosen optic is a critical part of it. The Mk22 Optic contract was awarded to Nightforce® (nightforceoptics.com).
I should mention at first, that the Mk22 Mod 0 has a top rail slope of 10 MIL (ECP), and the DoD MRAD has a 20 MOA slope.
In that separate contract, SOCOM chose the Nightforce MIL-SPEC ATACR™ (Advanced TACtical Rifle) in two flavors, both with 34mm tubes and Horus Vision TREMOR3™ reticles in MRADs. The example sent to us for testing was the MIL-SPEC ATACR 7-35×56 F1 with custom mount. The other option SOCOM chose is the MIL-SPEC ATACR 5-25×56 F1. “MIL-SPEC” indicates these scopes are not the commercial version of the ATACR; they must meet the MIL-SPEC.
While this author found shooting at 1,000 meters with the 35x was very helpful, the real end users generally only use the 25x level for engaging and having more field of view; the 35x end is used for observation.
Nightforce is well-known for the rock solid scopes they build—they’re made to go in the field. The reticles chosen for the ASR are First Focal Plane and of course etched on glass; as magnification is used the reticle will also be magnified. (The Second Focal Plane is behind the magnification lenses and stays at one grid size no matter the magnification—useful in some scenarios, but this author prefers FFP, target adjustments at range seem much more precise.) Nightforce optics are also well-known for their light transmission capability. Looking through a Nightforce optic is almost breathtaking in clarity; clearly this was a factor in SOCOM’s choice of the optic. One bit of lore from the end users—highly trained snipers—many have told this author that at extended ranges the Nightforce scopes are decidedly better at seeing deeper “into” shadow areas compared to other scopes, a function of the NF lens treatment. This is very hard to quantify, but many end users swear by this.
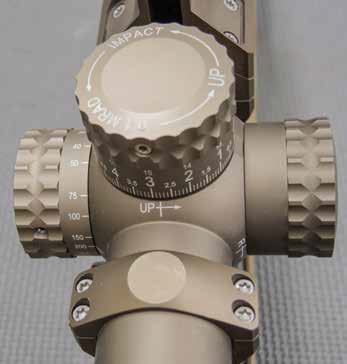

The mount chosen is the Nightforce MIL-SPEC UltraMount with the RAP-I Laser Rangefinder attachment bridge; a soft case is supplied. Nightforce supplies a tool kit for the Optic system, with some additional tools not in the ASR kit supplied by Barrett: Torque tools of 100 in-lb and 25 in-lb, as well as a T15 Torx head bit.
Note: The Nightforce MIL-SPEC ATACR described here was also selected for the US DoD MRAD in .300 PRC caliber.
The optic selected for the US Army PSR version of the MRAD was the Leupold Mark 5HD 5-25×56 with MIL Grid 4 Reticle.
Nightforce ATACR 7-35×56 F1
[su_table responsive=”yes”]
Magnification Range: | 7-35x |
Focal Plane: | First Focal Plane (F1/FFP) |
Body Tube Diameter: | 34mm |
Overall Length: | 16.0in/406mm |
Mounting Length: | 6.6in/167mm |
Weight: | 39.3oz/1113g |
Click Value: | .1 MRAD (or on MOA, .250 MOA) |
Internal Adjustment Range: | Elevation: 29 MRAD (100 MOA) Windage: 17 MRAD (60 MOA) |
Parallax Adjustment: | 11yds–∞ |
Eye Relief: | 3.6in/91mm |
Field of View: | 7x: 15.0ft/5.0m 35x: 3.4ft/1.1m |
Finish: | Tan; hardcoat anodize |
Exit Pupil: | 7x: 6.0mm; 35x: 1.6mm |
Illumination: | N/A |
Elevation Feature: | ZeroStop™ |
Power Throw Lever: | Standard |
[/su_table]
Suppression
There are many considerations regarding suppressors for rifles; suppression of noise is not the only one. From the outset, SOCOM knew there would be a compromise on sound reduction for the 7.62 and .300 Norma Magnum calibers if they wanted one suppressor to use on all the calibers and barrels in the Mk22 Mod 0 system. Barrett’s engineers knew this as well; the bore had to accommodate the largest diameter projectile. The alternative would be to carry two suppressors, but for the small decibel reduction gained, the weight gain to the system would not be worth it. Thus, SOCOM chose one suppressor—the AML338. Barrett makes excellent suppressors, the AM series thread onto the outer section of the patented muzzle brake with the DC series being threaded directly to the barrel. Obviously, the AM series won out. The AML338 suppressor is on the Mk22. The DoD MRAD has the AM338. The main difference is that the AML338 has a secondary lock and of course the color; AML338 is Coyote, AM338 is FDE.
[su_table responsive=”yes”]
Model: | AML338 Suppressor |
Caliber: | .338 and less |
Length: | 9.90in (252mm) |
Diameter: | 1.75in (50mm) |
Weight: | 1.29lb (0.65kg) |
Sound Reduction: | -23-28 dB |
Mount: | Barrett® Muzzle Brake Adaptor |
[/su_table]
Each of the Mk22 barrel muzzle brakes has an identical diameter threaded outer section, and the muzzle brake is actually designed with being part of the entry chamber of the suppressor in mind.
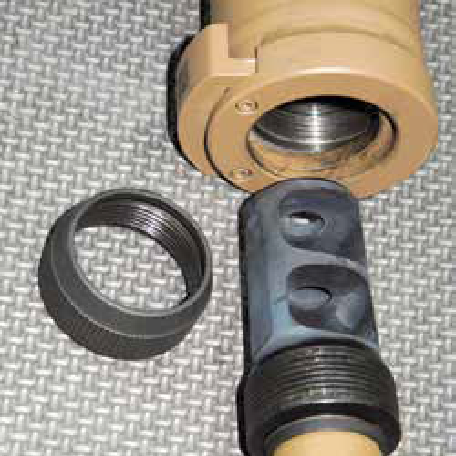
Where some loss of suppression occurs is that the AML338 has its bore diameter keyed to the .338-inch projectiles, and when the .308- or .300-inch (.300 Norma Magnum projectiles are actually a .308 diameter) projectiles are fired through, there is some blow-by that raises the decibel level. Honestly, to the ear it wasn’t very noticeable when we changed calibers. Then again, all of us who were shooting have high frequency hearing loss so the only way to really quantify it was using a proper meter like a Larson Davis 800B, which we did not have, and Dr. Philip H. “Doc” Dater wasn’t with us.
Barrett manufactures the AML338 suppressor out of a high-strength Titanium alloy. They use modern CNC machining and orbital welders to keep the hoop strength with the lowest amount of material. Precision bore alignment maintains accuracy, reduces point of impact shift and aids in flash reduction.
During our firing, we found that almost all of the groups tightened up when we fired suppressed. This phenomena is frequently observed in well-made, well-matched rifle systems. Doc Dater covers this in the Suppressor Class he teaches at Phoenix Defence, so I’m deferring to him on this:
This tightening up of a group happens the majority of the time as long as there is no misalignment. You also get a 20–50 ft/s velocity increase, not germane to this discussion. There are two factors in play. First is a change in barrel harmonics from the mass of the suppressor (and how tightly it is screwed on). Second (and probably a greater effect) is that on uncorking, the gas has approximately twice the velocity of the projectile and rushes around the bullet which then has to traverse the various shock waves that can cause a little instability. The can shears off this gas in the entrance chamber much in the way muzzle brakes do. The gas loses velocity quickly as it interacts with the air. Look at the three high-speed photos from a 20-inch barreled .223 gun.
[su_image_carousel source=”media: 83437,83438,83439″ limit=”3″ slides_style=”minimal” crop=”none” spacing=”no” captions=”yes” dots=”no” link=”lightbox” target=”self” image_size=”thumbnail”]
Per Doc Dater: “These were consecutive frames taken at 15,000 fps. The sun was just right so the lower image is a shadowgraph of the direct image above and better shows the shock waves. This series is used in my talk (with about eight other frames) as part of a flash study. The Mach disk is a high pressure, high temperature shock wave that actually ignites the carbon monoxide to make the fireball.”

Range Day 1: Intro to the Mk22
I’ve heard that government users have regularly seen groups in the sub-half minute range. Obviously, no one discusses the specifics of accuracy requirements or testing results other than what is put out publicly. Even if I knew, I would self-censor; we’re talking about national defense. I will say, that our testing confirmed the rumors.
SADJ is a firearms magazine—our writers and almost all of the staff are shooters of various levels and experience. Long-range shooting is a specific skill, and testing a rifle system like the Mk22 Mod 0 requires the person on the trigger to have the skill, not just be a “good shot.” Dennis Powell, a well-known civilian accurate shooter, joined us at the range for 3 of our days, along with long-range shooter Harry Bovie, Chuck Bolding, who is highly respected in training circles, Damon Bolding, a gunsmith at Phoenix Defence, and this author. Dennis was chosen by me to do the record shooting so I could hide my own deficiencies. We fired from bench; I did not want to get down and fire from “Rocking Horse Prone.”
Our chosen range? Boulder Rifle & Pistol Club in the high desert near Boulder City, Nevada. Excellent ranges, good people (brpc1.org).
Our first day at the range was learning the rifle. Before we started, we knew the rifle was coming in from another tester, so we had to bring it all back to zero and learn it from the start. By the end of the morning, we were hitting not-so-impressive groups at 100 yards and ringing the gong at 1,100 yards. Not time for serious shooting yet, time to study.
Range Day 2: Learning the Lessons
We went back to the shop at Phoenix Defence. We got out the manuals and filled in the blanks. This is a rifle, not a complex space station or mega-computer; it is a rifle system, however, and it takes study, trial and error to learn to make all the components perform at top level. This was a very boring day with Lessons Learned and studied out.
Range Day 3: Printing Paper 100
[su_custom_gallery source=”media: 83449,83450,83451″ limit=”3″ link=”lightbox” target=”blank” width=”140″ height=”180″ title=”always”]
[su_custom_gallery source=”media: 83454,83455,83456″ limit=”3″ link=”lightbox” target=”blank” width=”140″ height=”180″ title=”always”]
[su_custom_gallery source=”media: 83457,83458,83459″ limit=”3″ link=”lightbox” target=”blank” width=”140″ height=”180″ title=”always”]
After digesting the information for another week, it was back to the range. There were many sub-half-minute-of-angle groups, the best being a .300 Norma Magnum Berger 215-grain from a suppressed rifle—this was center to center under 0.3 inches. Very respectable group for Dennis. We now felt ready to take on the longer ranges.
Range Day 4: Long-Range Day
18 August 2020: Today was the day we’d been waiting for—we’d learned the system, and we were reaching out to 1,000-plus yards, for the record.





Conditions Day 4
Shooting times: 07:30-11:30
Pressure Hg: 27.66–27.71
Humidity: 22% down to 14% at 11:30
Wind: 5–8 MPH cross-range R-L
Temp: 96–110˚F
Elevation: 2,450ft
Vortex Razor Spotting Scope
Just as difficult as it is to be a sniper in the field without a spotter, it is the same at the range. Two sets of eyes work together and make the task quicker, and the feedback helps.

Vortex Optics has an excellent reputation; they gather light and give clarity that is at a top level. I’d honestly never looked through a spotting scope compared to this, too often the spotting scope is an afterthought on range day. Once you use the Razor® HD, and if you’re a serious shooter or end user, there’s no question of skimping on this essential tool again.
We had the availability of the Vortex Razor HD 27-60x85mm angled spotting scope with an MRAD reticle eyepiece. The reticle on the Vortex is MRAD, matching the MRAD system in the Mk22 optic. The Vortex has the ability to change to straight spotting with no reticle or to a reticle matching MOA if the optic being used is MOA. This is accomplished with an interchangeable eyepiece. Range can also be calculated easily with either reticle if there is an object of known dimensions in the field of view (vortexoptics.com).

MRAD vs. MOA? Without getting into a street fight like “9mm vs. .45ACP,” let’s keep it simple. SOCOM called for MRAD, and that’s what everyone is using. MOA is “Minute of Angle,” and old guys like your faithful correspondent usually use that. MOA is an angle measurement; in effect, 1 MOA at 100 yards is one inch. Take that to 1,000 yards, 1 MOA is 10 inches. MRAD stands for “Milliradians,” also a unit of measurement of angle. Lord help you if you have a scope in MRAD and other devices in MOA, you’ll be doing lots of unnecessary math in an already complex program such as long-range shooting. Both are based on the 360 degrees of a circle, and the discussed measurement is an arc that is a very small part of that circle when discussing accuracy in shooting. Without doing all the long division, at 1,000 meters, a one MOA click on your scope is 3.5 inches of adjustment on a target; and a one MRAD click on your scope is 3.9 inches. It makes a difference. Thus, if you’re using an MOA optic, make sure you have the MOA reticle eyepiece for your Razor HD spotting scope, and vice versa if you had the MRAD like we did in this test.
Vortex describes the Razor HD as having a “sophisticated triplet apochromatic lens system” and honestly, that’s a bunch of twenty-dollar words that don’t mean much to most people. Here’s basically what is being said: Triplet means there are three pieces of glass lined up; apochromatic means there isn’t any false color, shifting red and blue light to a different plane. Multiple lenses tend to shift colors and that has to be designed out. Thus, Vortex has the “sophisticated” job of getting three lenses to line up perfectly and stay there in long-term, rugged use, while keeping true color to the viewer’s eye—no small task with lens finish and refraction. This costs money, and the Razor HD is an expensive spotting scope, listing out at around $1,900. If you’re a professional, this is short money for what you are getting. Color can make all the difference in identifying targets and non-targets.

We used the Vortex PRO GT tripod to mount the spotting scope. It has a balance weight hook to the center, strong, lightweight legs and a very steady panning head.
The Vortex Razor HD 27-60x85mm spotting scope is under testing with many special operations groups, and we know it is currently with the Scout Sniper Section of Panther Team JMRC Operations Group in Germany.
Tools and Changing Calibers
As all men-at-arms know, you need the kit for your weapons. Tools, cleaning kit, gauges, and in a soldier’s kit, what is there has to be carefully considered regarding need, bulk and, of course, weight. SOCOM specifies the TO&E (Table of Organization & Equipment) it wants. The Fix It Sticks Torque Limiters (store.fixitsticks.com) are gaining in popularity, and SOCOM as well as Barrett and Nightforce call for this product in the inch-pound (in-lb) requirements. With this system, there is no need for carrying a torque wrench, each needed setting has its own torque limiter, preset and marked. These fit into any standard ¼-inch driver, including the Fix It Sticks T-Way T-Handle that is supplied, and any standard ¼-inch bit fits into the receptor end. The torque limiter will spin once the correct torque has been reached (within +/- 6%)—no over-torquing. Torque measurement is not required in removal, so no kit is needed for that (this is a measurement-only tool and not relevant here). I have not seen the Nightforce tool kit, but the Nightforce mount requires at least two things SOCOM did not dictate for Barrett’s contract: 100 in-lb torque limiter and a T15 Torx bit—I’ve no idea if Torx or Torx PLUS. I do know there was room in the Barrett supplied kit, so I added them for our field work.
Speaking of the Torx head screws and bits in the Barrett-issue kit, these are not regular Torx bits; they are Torx PLUS, denoted by the “IP” in front of the size, “IP30” instead of “T30” on a regular Torx. You can strip the star heads out of the bolts if you don’t use the PLUS bits. The lobes of the star points are more square on the PLUS heads, stronger than standard Torx and can handle more torque IF you use the correct bit. As noted by your faithful correspondent over the decades, nothing ruins quality firearms like a large hammer and a small mind.
The Mk22 Mod 0 Tool Kit
- 140-in-lb miniature torque limiter
- 65-in-lb miniature torque limiter
- 45-in-lb miniature torque limiter
- 25-in-lb miniature torque limiter
- 15-in-lb miniature torque limiter
- T-Way T-Handle Wrench
- 8 different bits (IP30 Torx, IP27 Torx, IP25 Torx, 5/32-inch hex, 1/8-inch hex, 5/64-inch hex, 1/16-inch hex) NOTE: The “IP” Torx are Torx PLUS!
- ½-inch socket and ¼-inch bit adapter set
- Deluxe zippered pouch with 3×5-inch Velcro® and MOLLE rigging on reverse
- 3 long Tekton® punches (1/16 inch, 3/32 inch, 1/8 inch) replacement parts 66061, 66063 and 66064
The only deficiency this writer saw in the kit was no “Snap Caps.” I like to train trigger release, and it’s not the healthiest thing for the firing pin to undergo unsupported release. If SOCOM wanted it, they would have specified and Barrett certainly could have provided. However, .300 and .338 Norma Magnum are not cartridges with COTS (Commercial Off-the-Shelf) snap cap availability. I used my standard A-Zone 7.62x51mm, but the .300 and .338 Norma Magnum cartridges have significantly shorter cases than .338 Lapua Magnum, and the bullets are seated deeper as well. The Norma cartridges have less taper, a slightly sharper shoulder and a slightly longer neck—once again, no COTS availability. I contacted the originator of the high-grade snap caps, Eric Kennard, from Harbour Arms. (harbourarms.com), and we discussed at length. I sent him some of the live rounds to work from, and within a few weeks he produced two of each for our use. Perfect. The custom work cost more than the COTS products he sells for almost every sniper/precision caliber, but it’s worth it. As a side note, Harbour Arms is a Disabled-First-Responder-owned company. I forwarded his contact to Barrett and SOCOM; hopefully there’s some support there—it would be nice to see Eric and Cindy get a shot at supplying.
Headspace Gauges
There were no headspace gauges supplied. They’re not needed at the operator level according to doctrine, even with all the barrel changing inherent to the system. I used my Pacific Tool & Gauge headspace gauges, PTG worked with Jimmie Sloan on the chambers, and Barrett used JGS Precision chamber reamers and gauges. It became clear early on that the Barrett MRAD system is virtually perfect. Our confidence in properly installing barrels and bolt heads went up immediately; this is a very reliable system.
Cleaning: The Right Way
[su_custom_gallery source=”media: 83473,83472″ limit=”3″ link=”lightbox” target=”blank” width=”220″ height=”170″ title=”never”]
Once the firearm is cleared, the upper receiver can be opened upward by pressing the release lever on the lower (note the silver lug). The bolt can then be removed to the rear, and the rear bolt guide and front bolt guide can be removed.




Bolt Disassembly




[su_custom_gallery source=”media: 83495,83496″ limit=”2″ link=”lightbox” width=”220″ height=”170″ title=”never”]
The bolt pin is pushed through—it can only go one way, and it is captured so it won’t come out. When you reach the proper position, the bolt will come out forward. Reassembly is the reverse.



Changing Calibers
[su_custom_gallery source=”media: 83501,83500″ limit=”2″ link=”lightbox” width=”220″ height=”170″ title=”never”]
Changing calibers is a simple yet precise operation. The barrels and bolt heads will be engraved with their caliber—match them up. Remove the magazine then the bolt as above, and change out the bolt head to the new caliber.
Unscrew the two barrel screws, but not completely. Remove the old barrel to the front and then slide in the new caliber barrel into the receiver; make sure the index pin at the top seats all the way. Starting with the rear screw, tighten the two barrel screws to 140 in-lb using the torque limiter marked for that and the T30 PLUS (IP30) bits. Be careful not to strip the screw heads. Assemble the firearm and ensure the bolt is properly rotating into position.
Changing Safety
The Mk22 Mod 0 has the same feature as the MRAD regarding the reversible safety selector. This is operator preference regarding safety manipulation. It’s a quick change.
With the upper and lower opened, the selector, in this case on the right, is moved to the halfway position between “safe” and “fire.” It will drop into a detent, enough to be felt. It is then pushed out to the selector side. Place it at the halfway position on the other side of the receiver and insert, then rotate to “safe.”
Forward Handguard
The Mk22 features the same M-LOK systems as the MRAD at 3, 6, and 9 o’clock positions, and some short Picatinny-style rails are supplied. In this case, the Harris 6–9 inch bipod can be seen with the LaRue Tactical® adapter and the rotating cant knob (not lever).
Case & Carry Bag
I’m not sure if the system hard case was chosen by Barrett or SOCOM. In any event, the Pelican™ 1770 is perfect. The system is laid out where all parts can be easily gotten to—this is a full system “Overseas Case” for deploying. Pelican paved the way on heavy-duty rolling hard cases and wasn’t afraid to work with the military. It’s heavy, but it’s not supposed to be dragged around in the field; it’s supposed to protect the equipment and nest it so it’s easy to visually ID a full system and choose needed components. The hard case is for the base camp (sorry, that’s old-speak—for the FOB). The soft case is for the field.
Armageddon™ Gear was chosen for the soft case for the Mk22 Mod 0 as well as the suppressor mirage cover. The stitching and bar-tack work are flawless. This is a very well-made case, and it is thought out for the end user, clearly by end users. The company’s advertising has some braggadocio, and I was skeptical, then I looked this case over carefully. Damn. Will Sonnett (Walter Brennan in “The Guns of Will Sonnet”) used to say “… and I’m better than both of ‘em—no brag, just fact,” referring to his sons and gunfighting. It’s pretty clear that the Mk22 case is based off of Armageddon Gear’s CSASS precision rifle case. To start with, that would be 1000D (Denier) CORDURA® fabric. Denier is the thickness of the textured nylon filaments used in the fabric. 1000D is very, very durable, for heavy duty uses—most soft cases use 500D or less. Armageddon uses a fabric that is solution-dyed which guarantees a homogenous color, and since this is a low-IR signature finish, that will be homogenous also. I spent a couple hours exploring all the ways to use the case, what I could put where, set it up for backpack with the straps and tried it as a drag bag. I carried it slung and used it rocking horse prone to keep the sharp desert pebbles from causing my delicate constitution discomfort. Seriously, this is long-time gear, versatile and well thought out. Excellent choice by SOCOM and Barrett, Armageddon Gear: “No brag, just fact” (armageddongear.com).
In Conclusion
I’ll keep it short and sweet. Barrett’s MRAD as the Mk22 Mod 0 is absolutely deserving of the award they received. We fired a significant amount of ammunition, suppressed and unsuppressed; changed calibers out numerous times and went between 100 and 1,100 yards. All of us were impressed. I don’t remember a discouraging comment, and as all shooters know, put a bunch of us together with a new system, and there will be grumping and carping. None at all with Mk22. SOCOM’s due diligence in testing is clearly optimum; without seeing the inside of their thought process, it’s clear the end results have paid off. From this humble correspondent’s view, the end users and procurement testing personnel at SOCOM have hit a clear home run with the Mk22 Mod 0 selection. I would bet that Barrett Firearms staff are proud of this (Nightforce as well!), and I would expect to see many follow-on contracts for this system by US end users, and especially the overseas SOF community taking advantage of the exhaustive testing done to adopt the Mk22. Bravo!