ABOVE: Third generation model Colt LE1020 successfully passing a mud test in 2008. Although never put into production, the final production LE6940P/APC is a direct descendent of the LE1020.
When looking at the overall number of manufacturers making AR-type rifles, very few of them are long stroke/short stroke piston variations. Some manufacturers such as LWRCI have made it their primary business to make rifles in this configuration. Going back to the early 2000’s when H&K brought out their HKM4/HK416 they touted it as being a revolutionary leap in technology. But where does the evolution of the external piston operated M16 begin? Go back to the early years of the Vietnam War for the answer. From 1966 to early 1968 the newly introduced AR-15/M16 and XM16E1 rifles began heavy use in combat. Although the Army had procured the “One time buy” and General Westmoreland requested that all American ground forces be armed with the new weapon, the Ordnance Corps, like many other times in the history of the US Army failed the American soldier. Secretary of Defense Robert McNamara ordered them to get a combat ready rifle into the hands of the Army and they disobeyed that order trying to keep Rock Island and Springfield Armory pumping out the M14 rifle, which was not optimum for jungle warfare. News reports came into the already skeptical American public that soldiers were dying next to faulty, malfunctioning AR-15 rifles. The soldiers lost confidence in their new state-of-the-art rifles and felt strongly about the superiority of the enemy AK47 rifle. From the troops’ perspective, they did not understand increased cyclic rate due to powder change, corroding of bore and chambers causing failures to extract or parts breakage due to high cyclic rate: he understood “My rifle does not work, and theirs does.”
At this time in 1967, a congressional sub-committee headed by Senator Richard Ichord convened to investigate the AR-15/M16 and all of the issues surrounding the procurement, rights to the technical data package, chain of events to milestone decisions and malfunctioning. Colt engineers went to work making a version of their AR-15/M16 rifle that would make use of the (perceived) more reliable long stroke piston of the AK47.
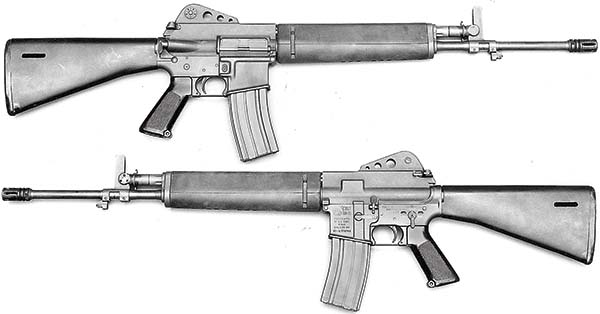
The Colt Model 703 was the first external piston operated rifle of the platform. For all intents and purposes the Model 703 left the ergonomics of the AR-15 and stuck an upper on it designed around a piston operated rifle. The lower receiver remained the same as the new upper receiver could retrofit any stock lower receiver. The prototype had the Foster Sturtevant designed four-position selector offering the shooter safe, semi-auto, auto and 2 or 3 round burst.
The Colt engineers back then realized the best way to make an external piston operated rifle was to redesign the upper receiver, not to take the current one designed for direct gas impingement and turn it into a host for an operating system it was not designed for. The bolt carrier has the long stroke operating rod/piston pinned to the top of the bolt carrier. The bolt carrier has two longitude grooves on the side that fit into two slots in the upper receiver acting as guides to keep the bolt carrier group moving straight back and forth in the receiver (no carrier tilt).
The gas system utilizes a gas regulator allowing the shooter to tune the rifle for any combination of ammunition type or environmental condition. Self-regulating gas systems are more finicky due to extremes of ammunition types, propellants, as well as weather and atmospheric conditions. Allowing this all to be regulated is an excellent solution. The problem is if an untrained user messes around with the regulator not knowing how to adjust it properly, the rifle may not function, and may beat itself up from over gassing or function unreliably. It has always been a double edged sword whether to permit the soldier access to adjust gas or take a self-regulating system and try to control the ammunition that goes into it.

Colt issued a report in May of 1969 titled Colt’s Automatic Rifle Model 703. The lead off into the report stated, “It is Colt’s belief that Colt’s Model 703 will demonstrate better performance and superior durability when compared to the M16/M16A1 rifle.” Nobody can be sure, all of the engineers who worked on this project are gone, but evidence points to the fact Colt was both involved in the investigation of what was in fact going wrong with the AR-15/M16 rifles in Vietnam but they also wanted to be ready with a solution if the problems pointed to the operating system of the AR-15/M16. It appears as though the Model 703 was a proactive step on Colt’s part.
According to the report, “Prototype Number 1 features a closed, adjustable gas system which is completely housed in the front sight assemble. This allows the user to optimize his weapon’s efficiency according to conditions dictated by climate or ammunition. No gas deposits are permitted to enter the breech mechanism and the result is a cleaner operating weapon. In addition, a larger extractor, a failure-free extractor spring and increased dwell time before unlocking have been incorporated.” The report also stated a list of features of the Model 703:
Better extraction through delayed unlocking and stronger extractor.
Top and side sling capability.
Adjustable gas system.
Burst control (2 or 3 rounds).
Buttstock stowage of cleaning equipment.
Simplified handguard disassembly.
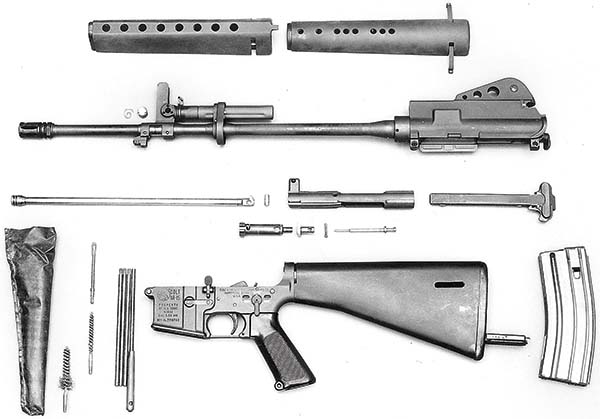
Also listed were Model 703 Advantages:
Gas is exhausted behind the front sight rather than into the bolt group thereby reducing the frequency of cleaning.
Weapon can be slung over the shoulder in the assault-ready position.
Adjustable gas system compensates for ammunition and climatic conditions.
Rate of fire remains relatively constant (within ± 15 rounds/minute) at any setting.
The rifle’s upper receiver was very cumbersome when compared to that of the direct gas rifle although it weighed only 4 ounces more. All stats were comparable to the M16/M16A1. However, this rifle was never let out of the gate.
At the same time, there was another organization looking to change the direct gas operating system to a short stroke tappet system. The contract, DAAG25-68-C-0742, was awarded to Olin Mathieson Chemical Corporation’s Winchester Western Division with the mandate to create a system to retrofit existing upper receivers with “The object of this contract is to improve the combat and operating effectiveness and reliability of the existing M16A1 rifle by developing a short-stroke gas system.”
The program objectives consisted of:
Determining the functioning characteristics of 25 unmodified M16A1 rifles.
Designing a test rig to establish parameters for a short-stroke gas system.
Testing and developing two prototype short-stroke gas systems.
Conducting a 6,000 round test, with Government surveillance, on three Short-Stroke models for delivery to the Government.
Fabricating ten Short-Stroke Models for delivery to the Government.
Estimating contractor cost for retrofitting M16A1 rifles with short-stroke gas system.
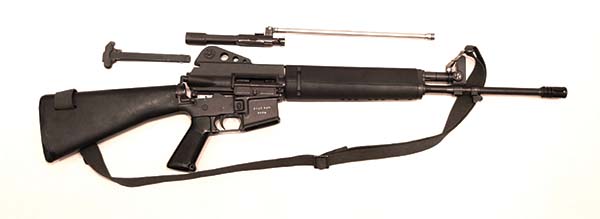
“It is concluded from this program that the short-stroke gas system is functionally a practical system for the M16 Rifle and will significantly enhance the operating effectiveness and reliability of this rifle.”
The control rifles were 25 government furnished M16A1 rifles with the new and improved sliding weight buffers and the early non chrome lined bore/chambers. It should be noted a major issue with the reliability of the M16 in Vietnam was in fact due to the non-chroming of the chamber of the rifles. The corrosion and pitting caused a majority of the failures to extract, which were catastrophic in combat. The only way to remove the stuck cartridge case was to knock it out with a cleaning rod. Once the chamber was corroded there was not enough cleaning possible to correct the failure to extract. The barrel would have to be replaced.
The gas cylinder location was to be located 5.5 inches forward of the bolt face. The original gas port location was not used for several reasons including the need for a complete redesign and replacement of the already pinned on and costly front sight base. Additionally, a long flexible gas piston would be susceptible to damage in handling and usage, the gas piston falling outside of the handguard cap and forward portion of the handguard and probably most important was the gas to be tapped at an inconsistent low pressure portion of the pressure-time curve. The shorter gas system would permit a short and sturdy gas system and tap consistently high pressure portion of the pressure-time curve. The new gas block would be pinned to the barrel for stability and durability under the hand guard. The gas block consisted of gas cylinder housing, housing plug and utilized a plain piston. There was a new gas port drilled. The bolt carrier was modified with a solid carrier key that was reinforced by a carrier key pin that was copper brazed to the carrier key. The pin is inserted into the existing gas hole in the carrier and the carrier key screws were torqued and staked. A chamfered cam pin or a steel insert in the receiver is required to overcome peening of the receiver at the rear corner of the clearance cut for the cam pin rotation. This peening is the result of the cam pin impacting on the cam in the bolt carrier after bolt pickup and rotating into the receiver. The final design omitted the chamfer of the cam pin and opted for the steel insert, which is basically a steel screw that prevents the cam pin from damaging the aluminum receiver. There is a hole drilled in the upper receiver, on the left side where the hump is, where the cam slot is on the receiver and the screw inserted.

The result of the study concluded that material cost per rifle was $4.16 and labor costs (excluding burden) would be $4.13 per rifle. The value of machinery, tools and gages required (incl. benches, heat treatment and Parkerizing equipment) would be $2,064,000 and the contractor start-up costs would be $205,000. The conclusion of the contract is as follows:
The dynamic operating characteristics of the M16 rifle can be duplicated with a short-stroke gas system.
The short-stroke gas system will substantially eliminate those malfunctions associated with fouling, i.e. failure to fully open and fully close.
The M16A1 rifle with a short-stroke gas system is capable of firing a significantly larger number of rounds without cleaning and lubricating than the standard M16A1 rifle.
Information to date indicates that functionally the short-stroke gas system is a practical system for the M16A1 rifle.
Certain functional characteristics, including “fail to fire” and “fail to eject” are independent of the operating energy source (gas system), but are sensitive to other mechanical conditions.
A substantial amount of data has been generated that would be useful in further analysis of the M16A1 rifle system.
Like the results of the Colt Model 703 development, the retro fit program was quite viable. However, neither system was destined to replace that of the AR-15/M16 rifle. The findings of the numerous investigations showed what the root causes in the malfunctions were in Vietnam. In reality it was not a deficiency in the rifle system, in fact it was a good viable system destined to become one of the most prolific combat rifles of all time. It was found that the major problem, failure to extract, was caused by a combination of failing to chrome plate the chamber as well as lack of cleaning tools to maintain the rifle. Along with this there was no instruction on maintenance of the rifle. The other major issue was the untested and quantified decision to switch from IMR to Ball powder against the advice from both Gene Stoner and Colt’s. In a nutshell, the rifle could work reliably with ball propellant if it was in fact modified to do so, which is what was done: the change from a basic spring guide to a buffer that had sliding weights to prevent light strikes due to bolt carrier bounce and shot peening the bolts to increase its strength due to the higher cyclic rate that cause bolt breakage. Also, the firing pin was lightened and the disconnector strengthened. With all of these modifications there was little to no benefit in going backwards to the external pistol. The direct gas system would go on to prove itself in the late 1960s right up through the introduction of the M4. There was no further military interest in a new gas system. Although Rhino offered a retrofit kit for commercial sales in the 1980s, it never really gained momentum.
Right after the initial years of Gulf War 2, combat missions by Special Forces showed the newly introduced M4 carbine was about to go from a back-up rifle for those who had jobs that did not require the full length rifle but needed more than a pistol could provide, to a preferred primary combat rifle by SOCOM as well as regular Army. In the early days, SOCCOM began to experience failures of bolt breakage, and barrels rupturing, as well as failure to extract. Oddly enough, regular Army was not seeing the same issues. These reports let way into the HKM4/HK416 program that claimed to create a retrofit kit as well as a new rifle touted to “improve” combat reliability of the M4 by use of a short-stroke tappet operating mechanism. So literally the HKM4/HK416 upper receiver conversion was designed initially for SOCOM to help with their perceived problems with the M4. SOCOM had decided they needed their own rifle, not one that the Department of the Army was project manager of, which included the XM-29 program that would later be whittled down to the XM8, but one they fully controlled. SOCOM in no way wanted a weapon that was an Army weapons program – hence the commencement of the SCAR Special operations Combat Assault Rifle Program. It was also no secret that the Army did not want the SOCOM SCAR rifle; they wanted the XM8. With both rifle programs running consecutively, there was a race to get the SCAR rifle adopted before the Army could get the XM8 adopted. In the end, the XM8 program was cancelled. Any manufacturer of firearms who wanted a piece of the government sales knew the M4 was sole source from the U.S. Govt. to Colt and that the Army was happy. The only way to get into the U.S. military market was to say what they had was deficient and to open up the market to non-Colt M4 rifles.
Everybody knew that SOCOM was looking for an external piston operated rifle although it was not written that way. Colt was willing and ready to partake in the competition. They, however, would introduce and submit 3 rifles to the competition; two of which were their well proven and tested direct gas variations and the third would be Colt’s first external operated piston rifle since the Model 703 and that was in 1969. At the same time, both the government and Colt were looking into the issues with the rifle failures that SOCOM had. Was it a defect in the rifle design, quality, or was it user induced. Regardless of this outcome SOCOM wanted their own rifle.

Colt submitted three rifles to the SCAR competition. Both types, A and B, were based on their combat proven direct gas system. The Type C was based on the short stroke tappet piston system. The system is simple and robust. There is an operating rod with a return spring attached, a piston and a gas cylinder sleeve. All this was held into the Type C rifle with a roll pin. Due to time constraints the roll pin was not removable for cleaning at the user level. The piston head had a tapered cone shape to it rather than the conventional flat shape. The upper receiver was the newly developed monolithic upper receiver with removable bottom rail to allow installation of the M203 grenade launcher. The carrier key was solid with no gas holes and part of the bolt carrier was machined to install the carrier key. The entire rifle was coated in UCT (Ultra Chem Tech), which is a nickel boron coating and then painted tan as per the specification. The piston operating system required an H2 buffer. The rifle used a unique and patented short throw ambidextrous selector lever and a Norgon ambidextrous magazine catch. There was an Otis Technology grip cleaning kit installed and a VLTOR modstock. The front sight base had a folding front sight that engaged and disengaged by a detent.
The Type C faired very well in the competition. Sources claim it was number two in the selection. The winner was the FN rifle. There were lessons learned by Colt from feedback on the Type C rifle that would assist them in further refinement of their piston rifle. The industry was calling upon Colt to produce an external piston operated rifle. There was growing demand in the international market for something to compete with the HK416.

In the secrecy that Colt is known for, they went to work on their next generation piston rifle in the 2007 time frame. This new rifle would be called the LE1020. The first major change was to have a way the operating rod and grooved piston could be removed at the user level for cleaning. On the front sight base was added a captive pin similar to that of the takedown and front pivot pin. This made it simple to remove and install. Also, to cut down on parts that could be lost, the piston was attached to the operating rod. The carrier key was simplified as well. A dowel pin was added so a standard bolt carrier could be used. The dowel pin went into a hole drilled into the gas slot in the top of the carrier and drilled into the bottom of the carrier key and the carrier key was held in place by two carrier key screws. The intent of the dowel pin was to take all of the stresses off of the carrier key screws. Barrels were offered in 10.5, 14.5 and 16.1 inches. The lower receiver went back to the standard lower receiver. The UCT finish was dropped in favor of standard Mil-Spec hard coat anodizing as well as manganese phosphate on the bolt carrier group and barrel. From 2007 to 2010, the LE1020 made its way into all the major trade shows in both the military and commercial arena. The LE1020 got a significant amount of attention from both attendees and press at SHOT Show and Colt was flooded with phone calls from customers regarding the high demand for the Colt piston rifle. At this time the controversy was in clear swing as to the question if the U.S. military is giving their warriors the best small arms available in the world. Colt’s resources were heavily involved in that fight. It is this author’s opinion that Colt higher management felt that if they introduced an external piston operated rifle, it would be an admission that their M4 was inferior. Perhaps in hindsight this author feels the better way to look at it would have been to give the customer what they asked for rather than give the business away to another company.
In 2009, Colt released for sale their first monolithic upper receiver but in the direct gas configuration called the LE6940. As expected, the rifle was an instant success. It also was the first new rifle introduced by Colt since the LE6920, which was
in the late 1990s.
In 2010, Colt introduced to the military market their refined LE1020 as the APC or Advanced Piston Carbine and for the LE market as the LE6940P. The biggest change between the LE1020 and the APC/LE6940P is the operating rod/piston. The new system was called an articulating link piston. This pivoting piston and op-rod connection compensates for deflection of the barrel during firing and due to thermal expansion. It also reduces recoil and muzzle climb during firing with the piston system closer to the bore. On the end of the piston are gas rings to seal the expansion chamber. The face of the piston is flat rather than tapered cone shaped as
was the LE1020.

Added to the upper receiver is the steel insert behind the cam slot to prevent damage to the receiver. This is the same in concept to what Winchester-Western did in 1968 but Colt further refined the design to make it that much more effective
than the original.
After getting customer feedback, Colt modified the folding front sight base with a sliding lock. Customer comments came in that if they were to bump the front sight the sight would disengage causing them issues with engaging targets. Colt put a durable sliding lock that prevented this from happening.
Further testing on durability showed that the current bolt carrier design could be improved. Heavy usage showed that even with the dowel pin locating the bolt carrier key on the bolt carrier, upward recoil stresses on the carrier key screws allowed them and the dowel pin to break. Colt decided to switch to an integral bolt carrier/carrier key design with the impact area of the operating rod being on the face of the shortened integral carrier key portion of the bolt carrier. This eliminated this problem from happening.
The APC was submitted to the Individual Carbine competition. There were modifications to the lower receiver to make the rifle fully ambidextrous. The lower receiver was the new 7.62x51mm modular LE901 lower receiver with the ambidextrous bolt and magazine release. The front of the receiver was cut back to a 5.56mm configuration. The Colt entry was one of the finalists but the Individual Carbine program was cancelled due to nothing showing a significant increase in reliability over the standard M4. It is this author’s opinion that the testing in the IC program was flawed. They tested to the same 6,000 round protocol as they used for the M4. Of course they will see no major improvement. Perhaps if they pushed it out to 12,000 rounds they may have seen some significant improvements. But as the saying goes, the best is the enemy of good enough. According to the Army the M4 with its product improvement features is fully suitable for the Army. There is no requirement for anything to exceed those specifications.

The current APC/LE6940P rifles are what you have come to expect from Colt – durable workhorses that one can bet their life on. The APC will surely have a future in the international market and is in fact involved in testing in several countries. Unfortunately, it is the new kid on the block competing with piston operated AR rifles that have been in the field and refined for more than a decade. In time the Colt rifle will achieve a combat record and prove itself the way all of its predecessors have for the last 50 years, on the battle field.





